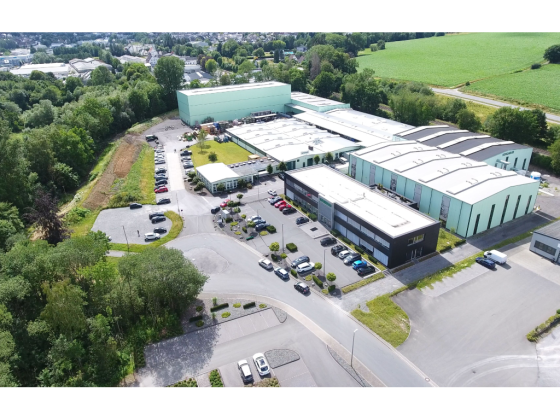
As many industries emerge from the global Covid-19 lockdown, Torque Magazine's Liberty Sheldon visited Kohlhage Gmbh at its base in Neuenrade to discuss how the family company has united four divisions under one Kohlhage umbrella…
Based in Neuenrade Germany, leading fastener supplier Kohlhage puts family first as they have become a fully family owned business once again after the Kohlhage family obtained full shares in the company earlier this year. Additionally, the company have decided to combine all four divisions under one Kohlhage umbrella to further develop its customer base and emphasise their potential as a global business.
The company’s four divisions; Kohlhage Automotive, Kohlhage Kunshan (a subsidiary of automotive in China), Kohlhage E-Tech, Kohlhage Fasteners, deal with a variety of markets such as the automotive industry, general engineering, plastics industry, and fasteners.
Marc Schreiber, Kohlhage’s Managing Director says: “We have decided to unite the four divisions under one group as a way of reducing cost and making more efficient sales. We also believe the change will improve our knowledge exchange in areas such as welding as many divisions such as Kohlhage Automotive and E-tech are considered welding specialists. We also aim to be much faster, stronger, and more competitive for our customers.”
“Now we are communicating Kohlhage as a brand and a group with different divisions, we want our customers to know that we are Kohlhage, and you will never see a company with more potential,” adds Tobias Schneider, Head of Sales.
History
Founded in 1929 by Ernst Kohlhage, the company originally focused on screws, nuts, and electrical material. With a team of advanced specialists and roughly 200 employees, 2019 saw Kohlhage generate a turnover of 42 million euros.
After the death of its founder, Kohlhage was taken over by Friedrich-Wilhelm Kohlhage, the son of original founder Ernst Kohlhage who developed the company and expanded its production size considerably. In 1974, Friedrich-Wilhelm Kohlhage purchased 22,000 square metres of land in Küntrop and later another 8,000 square meters. The company’s production facilities moved to the new production hall in 1979.
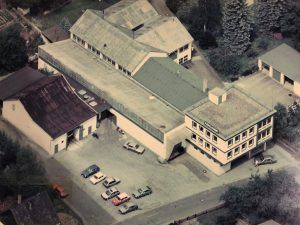
In order for production and trading departments to evolve, in 1989, Kohlhage separated departments and stopped cross trading in the company. Kohlhage Verbindungstechnik, the manufacturing side of the company, moved to Küntrop with 70 employees, while Kohlhage GmbH remained at the old location with 20 employees.
Additionally, Michael Stock joined Kohlhage in 1989 as its second Managing Director and share holder, and after the retirement of Friedrich-Wilhelm Kohlhage, took over sole management of the company. Under Stock’s leadership, the entire company moved to Küntrop and the old company location was dissolved in 1997.
The Kohlhage family remained present in the company despite the change in management and had a 49% shareholding. However, 2020 saw the Kohlhage family completely take over the company’s shares in the business and has since been represented by Maximilian Schreiber, the great-grandson of Kohlhage’s founder
Fasteners
The company’s Fastener division is currently the largest division under the Kohlhage umbrella, its competencies include inserts, weld nut welding screws, cold formed parts, stamped parts and turned parts. Additionally, Kohlhage provides camera sorting in house up to 10PPM.
Within Kohlhage Fasteners, a particular focus is placed on cold forming and stamping processes. Cold forming involves sections of wire that are formed under pressure in two or more stages without the use of heat. The process allows for high production speed and the optimal use of material as the percentage of material loss is only 10-15% in comparison to material losses of up to 50% and more in turning and punching processes. Furthermore, the stamping process is ideal for large quantities of products and is the most economical. The machines can run at 500 stamps per minute and more, depending on thickness and complexity of the parts.
Tobias Schneider, Head of Sales comments: “Kohlhage is known for its impressive global supply chain management. Our customers know we are a trading company with our production taking place in Europe and Asia. We have ensured that we know where to go to get the best products, for the best price, with the best quality for our customers.”
With an annual division turnover or 17.4 million euros, Kohlhage have transitioned from a company originally focusing on distribution of standard parts to customer specific development and component design.
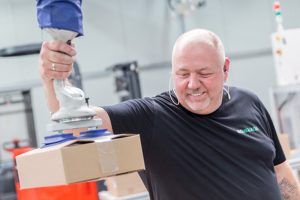
Due to the company’s vast technical knowledge and expertise, it is able to work closely with clients to optimise specialised products, whilst producing this with the same amount of precision as original standard parts. The company focuses on advising customers with 90% of products now customised for clients.
“We try to understand what the article is for and try to optimise this with the customer to get the best product available to them,” continues Schneider.
New projects are underway for Kohlhage Fasteners, says Marc Schreiber. The company is designing products such as a special pin for steering systems, special fasteners for seat systems and c-parts logistic for an international supplier for the automotive industry. Furthermore, the company has invested in two new sorting machines used for fasteners and special tubes.
Other divisions
Kohlhage Automotive
A high level of technical competence, its own purchasing office in Asia, 100% in house inspection of mass- produced fasteners and a new warehouse with over 10,000 pallets, highlights Kohlhage as a respected partner in the automotive industry.
The automotive division prides itself on its consulting competence and flexibility as they work closely with their clients throughout the development process. For example, the company’s advanced expertise allows technicians to work closely with clients to design geometries with process reliability from an early stage. This has enabled Kohlhage Automotive to be known as experts by several global automobile manufacturers.
The company are currently reorganising its production flow with new machine investments. New products are also being developed for globally recognised automotive companies. For example, Kohlhage is featuring a new cooling tube for power electronics for BMW, and an oil tube for a turbocharger for Voltswagen.
Kohlhage Tubes Kunshan
As the automotive industry continues to develop in Asia, Kohlhage jumped at the opportunity to open a production facility in Kunshan in 2016. Located in East China between Shanghai and Wuxi, Kohlhage has a 450m2 production facility with a total of 11 employees. Kohlhage experts based in Neuenrade train employees and control production so that all products manufactured in Kunshan can bear the Kohlhage stamp for exceptional quality. Furthermore, Kohlhage is also looking to develop the brand beyond conventional e-mobility as they are working to design solutions for hydrogen tanks and fuel cells.
Kohlhage E-tech:
Founded in 2018, Kohlhage E-Tech is the youngest of all four divisions with a total of 80 employees. The division works in collaboration with Kohlhage Automotive to developing individual solutions for electrically powered vehicles.
Covid-19
As we approach the six-month mark since the beginning of coronavirus lockdowns across the globe, travel restrictions have begun to lessen and the fastener industry is back on its feet after major hits to the automotive industry and more.
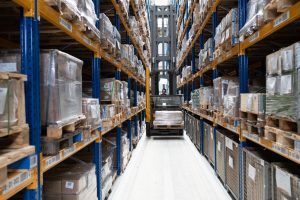
The Kohlhage group is continuously evolving and expanding to suit current climates. The company discussed its advantage during coronavirus as they already had the product stored in advance and therefore, did not have to source from Asia.
“We also buy worldwide,” says Marc Schreiber. “And our containers also take just as long to get here from the Far East, about six weeks. But there is something that sets us apart from most companies that also buy in Asia: We operate a large high-bay warehouse here at the Neuenrade location. We only rebuilt it last year, thus multiplying our storage and logistics capacities. That is why the products that our customers will need tomorrow are here today. Some have been for months. We always plan in such a way that we have a stock that covers the needs of around three months. Our customers benefit from this. Because they can assume that we will deliver their products exactly when they are needed. It has been working for many years. And at the moment it works all the more: Our customers don't have to ask us whether we can deliver. They just know that we can."
When asked what is to come for the future of Kohlhage, Schreiber states: “We want to be one of the best in quality, technical demand and pricing in our branches. That means continued growth for Kohlhage Fasteners, developing new parts and finding new high potential customers. At Kohlhage Automotive and E-Tech we want to be considered as a highly regarded technician specialist for tube bending and welding assemblies for the automotive industry.”
To conclude its impressive array of future plans and new projects, the company has recently finalised a new logistics process and is looking forward to attending plenty of exhibitions post Covid-19. “For the next year we plan to attend in different exhibitions like Fastener Fair or IZB Wolfsburg. We also want to push our partnership ‘Expertise Sauerland’.”
If you are in the fixing, fastener tools and distribution industry you can subscribe to Torque Magazine or sign up to our weekly newsletter.