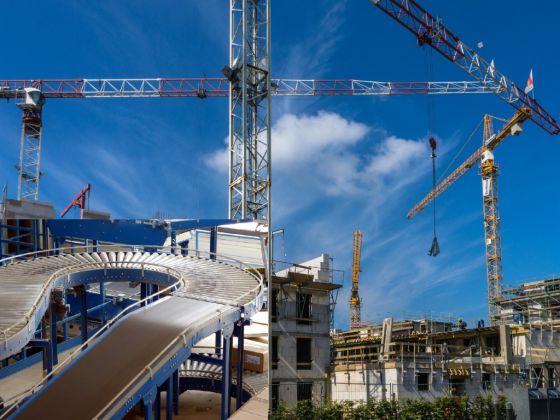
The construction site is changing, with implications for product suppliers and the supply chain…
Just in Time (JIT), traceability and zero defects are concepts familiar to production lines the world over and there have been no shortage of attempts to bring those learnings and concepts to other settings, including the building and construction site.
Hilti is among those making headway. Earlier this year, the firm unveiled its smart traceable fasteners for construction sites. Using digital documentation, every smart fastener is uniquely identifiable and traceable, allowing users to scan a code with a smartphone and view the installed fastener details, certifications, inspection documents and more. If “connected anchors” all sounds a bit cutting edge, then it is worth bearing in mind that Hilti is not alone in working towards the goal of making construction projects more closely resemble advanced production lines.
Construction transformation
Coventry’s Manufacturing Technology Centre (MTC) has begun work on a newly‐awarded project which aims to transform how domestic buildings are designed, manufactured, and delivered in the UK.
The project – IGNITE – is part of a suite of key projects awarded to the MTC, which are part of the Transforming Construction sector deal initiative, funded through Innovate UK.
IGNITE will create digital tools to support the transformation of the construction domestic supply chain. It is led by Places for People Group with consortium members LYNQ Ltd, Totally Modular Ltd, Northmill Associates Ltd, ModularWise Ltd and Project Etopia UK Ltd. Project delivery starts July 2020 for delivery in April 2022.
“The overall aim of the project is to develop an end‐to‐end digital platform which integrates design outputs, on and offsite programme activities, and supply chain readiness,” says Susan Hone‐Brookes, chief engineer at the MTC. “We think of it as bringing the learning of the automotive sector, with their car production flow lines and just‐in‐time supply chain integration to the construction sector. Creating a digital portal to share options for housing developments will enable developers and construction supply chains to gear up in a more strategic way, unlocking value through optimisation of manufacturing processes and understanding economies of scale.”
IGNITE will introduce a tendering process to enable housing providers and developers to obtain prices from across modular manufacturing companies in one sweep. They can then shortlist or move forward from that information. This can potentially save months off a project’s lead time as well as the costs associated with the current process, so says the MTC.
IGNITE will also enable developers to influence the manufacturing supply chain by procuring the same housing product across different modular manufacturing companies, so efficiencies can be achieved and better prices negotiated on manufacturers’ products, reducing the overall cost of the homes.
Julie Alexander, director of technology and innovation for Places for People, adds: “Project IGNITE will create a new digital toolset that will allow developers to regain control of house designs across the modular manufacturing company supply chain. House builders that retain assets, such as in the regulated housing sector, require more input into the design of the products being procured to ensure they meet the needs of their customers. Project IGNITE will allow this to happen.
“Developers will also get more visibility of the in‐factory manufacturing process allowing them better financial control over modern methods of construction projects. The project will also ensure that all houses being procured will be delivered with a digital twin, critical for the future of asset management.”
The MTC is a key member of the Construction Innovation Hub ‐ an alliance of experts in manufacturing, digital, building performance standards and construction technology to drive innovation and technological advances in the construction and infrastructure sectors (see below).
The MTC was founded by the University of Birmingham, Loughborough University, the University of Nottingham and TWI Ltd. The MTC’s industrial members include some of the UK’s major global manufacturers. The MTC aims to provide a competitive environment to bridge the gap between university‐based research and the development of innovative manufacturing solutions, in line with the Government’s manufacturing strategy. The MTC is part of the High Value Manufacturing Catapult, supported by Innovate UK.
“A BETTER BUILT ENVIRONMENT”
Aiming to transform the UK construction industry, the Construction Innovation Hub is funded by UK Research and Innovation through the Industrial Strategy Challenge Fund.
“Working around the four core themes of Value, Manufacturing, Assurance and Digital, we are changing the way buildings and infrastructure are designed, manufactured, integrated and connected within our built environment.”
“The Hub will develop the next stage of building information management (BIM) processes, tools and standards for the whole lifecycle of an asset. The Hub will develop new digital approaches to quality control, testing and validation, and regulatory compliance…
“The Construction Innovation Hub aims to enable buildings to be built faster, more sustainably and more economically. These buildings will go on to perform better in terms of ongoing running costs as well as social and environmental outcomes.”