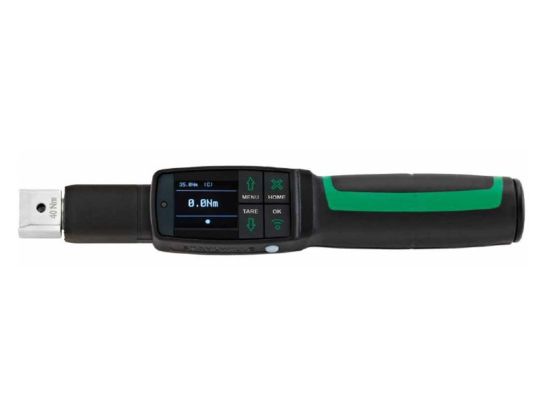
With 150 years experience of hand tool development, Stahlwille has gathered generations of expertise and experiences in the field of tool systems and intelligent torque technology. Here, the specialist shares some of its knowledge...
Accuracy is everything when it comes to torque wrenches. If you want to avoid defects and problems on the production line, garage or anywhere else, ensuring that the correct torque is applied to bolted joints is vital, not least in safety critical applications. Thankfully, Stahlwille is aware of the pitfalls and helps customers avoid them with some carefully crafted solutions.
FLEXIBLE ROD REDUCES USER EFFORT
For example, traditional mechanical compression spring wrenches have a disadvantage in that users must remember to reset them to zero (or the smallest value that can be set) after use, to prevent the spring from becoming deformed – or risk the wrench inaccurately measuring torque.
Stahlwille has cleverly designed this problem out with its unique Flexible Rod system, which does not contain a spring. By jettisoning the spring, Stahlwille’s Flexible Rod doesn’t just provide a more reliable torque application (particularly when switching between torque settings) but also provides a longer service life, saving money for customers.
What is the Flexible Rod system, you ask? It uses a time-honoured principle that if the lever (in this case the flexible rod) is short then more force is required to overcome the resistance. The user moves the setting slide to modify the position of the counter bearing and in doing so changes the effective length of the lever arm (the Flexible Rod), thus increasing its resistance. A specific force is needed to overcome the resistance, which depends on the torque that has been set.
As soon as this point is reached, the switching element will be able to continue to travel and will produce both an audible and tactile signal – or “click”. Crucially, the tool components automatically return to their unloaded positions after the user ceases to apply force, avoiding the need to manually reset to zero, reducing errors and reducing user effort.
GETTING THE RIGHT ANGLE FOR SAFETY-CRITICAL APPLICATIONS
While accuracy in torque assembly is always important, for certain industries and instances with safety critical applications, precision becomes ever more vital. In these instances, it’s not just the torque applied that is controlled. Torque-angle tightening is where the fastener in question is to be rotated through a predefined angle after the snug point (or pre‐load torque threshold) has been reached. The snug points and angles are calculated prior to assembly so they can be applied repeatedly for bolted connections under constant conditions.
Reproducing clamping forces exactly is the aim of the game, this is where Stahlwille steps in with a solution for this complex process.
Stahlwille’s MANOSKOP 714 is an angle‐controlled torque wrench. It has four measuring modes; torque, angle (with torque pre‐load), torque backed up by angle and angle backed up by torque. What’s more, this electromechanical torque wrench uses Stahlwille’s cunning electromechanical technology, so not only does it provide precise, electronic tracking but also the classic ‘Click & Slip’ of mechanical torque wrenches. The tightening action is evaluated visually on the high‐res
OLED display and lateral LEDS – and is also indicated acoustically. The MANOSKOP can also log tightening actions which can be downloaded for evaluation and analysis, and complex fastener settings and sequences can be pre‐programmed for selection by the operator.
STAHLWILLE ON NEXT LEVEL TORQUE:
INDUSTRY 4.0 WORKPLACES AND NETWORKABLE TOOLS
DAPTIQ is Stahlwille’s label for interconnectable systems; tools that communicate with each other as well as with the controlling and monitoring systems of the work environment. Benefiting customers and users with greater efficiency and capability, Stahlwille’s smart solutions are geared up for digitalisation and Industry 4.0, with error proofing and safety continuing to be the name of the game.
In practice, this means the user doesn’t have to fiddle with settings and can concentrate on the task in hand with the likes of Stahlwille’s MANOSKOP 766 DAPTIQ angle‐controlled torque wrench. Production runs more efficiently, human error is minimised, training requirements are reduced, and a consistent high product quality is achieved through the clever tech.
This article was first published in the September 2021 issue of Torque Magazine. There's more on Stahlwille's next level smart torque technology in the November issue. In addition, Stahlwille has an online knowledge portal – named Spectrum – explaining the topics in this article (and more) in far greater depth. Find that at: www.stahlwille.de/en/news/spectrum and there's more on Stahlwille on the Torque site.