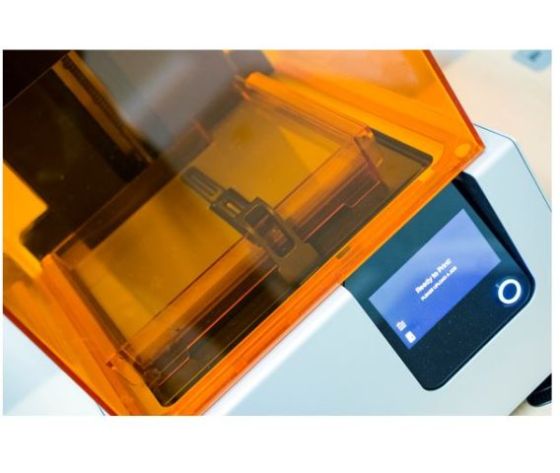
Global fastenings manufacturer and distributor TR Fastenings has invested in a new 3D printer.
The printer is an SLA (StereoLithic Apparatus) machine which reportedly delivers a far superior quality to the FDM (Fused Deposit Modelling) equipment replacing the existing model.
Until recently, SLA printing was prohibitively expensive, but after a group of American MIT students designed and received funding for the ‘Form 1’ model, costs reduced. The Form 1 machine has now been replaced by the Form 2 model, which TR has purchased.
While most of the components supplied by TR to its customers are metal, plastic prototypes are ideal to check the form rather than the function of a part. The printer will be used to create these prototypes for TR customers who want to explore new variations on existing parts or components used in their production process. The TR team will use its extensive library of CAD designs along with the printer’s sophisticated software to create variations of different fasteners for customers to view and test.
Keith Gibb, Head of Web Development at TR, commented: “We first invested in 3D printing technology 3 years ago by purchasing the FDM machine, which is simple to use and ideal for our first foray into the process but doesn’t produce the best quality parts.
“The speed and accuracy of the new printer has already allowed us to produce prototypes for a number of customers in both the automotive and electronics sectors. We made plastic prototypes of metal parts which meant one customer could check fit and form of a new part in 3 days rather than laying down expensive tooling and waiting for weeks. We’ve also produced fully working prototypes of injection moulded parts that were with the customer in 24 hours – the actual injection moulded samples would have taken six weeks.”
There's more from TR Fastenings in the latest edition of Torque Magazine. Subscribe today to make sure you receive future issues or flick through the magazine online on our archive.
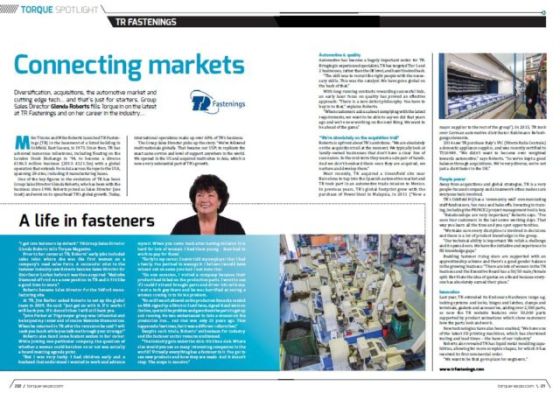