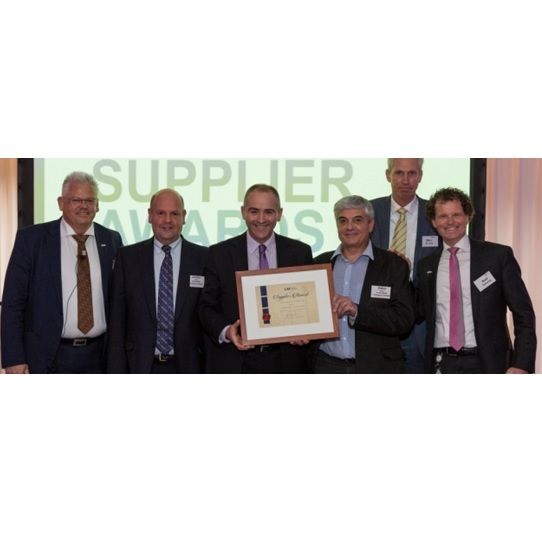
LM Wind Power has presented Scott Bader with its 'Most innovative supplier 2016' award.
Scott Bader's new 'zero styrene' spray gelcoat technology came in for praise from the wind turbine rotor blade supplier.
LM is a long standing global customer of the company, with factories using Scott Bader's gelcoat and structural adhesive in the production of FRP wind turbine blades.
“Scott Bader is absolutely delighted to receive this recognition of our innovative capabilities from a major customer like LM Wind Power," said Malcolm Forsyth, Director of Global Strategy for Scott Bader. "We dedicate more than 10% of our global workforce to research and development (R & D), and see innovation and bringing new advanced technology products to market as a key corporate strength and competitive differentiator. The Scott Bader R & D team rose to the challenge set by LM Wind Power to rapidly develop a zero styrene gelcoat for blade manufacture and did a fantastic job in developing this new breakthrough product in a short period of time."
This latest in-house R & D innovation from Scott Bader was in response to LM Wind Power’s HSE and sustainability objectives, set with the full support and participation of senior management within LM Wind Power. Marc van Heeringen, Supply Chain leader for Chemicals at LM Wind Powe, said: “In LM Wind Power, we have an internal Global HSE & Sustainability Council chaired by our CEO. A key sustainable development goal agreed by the council is to eliminate styrene from all LM Wind Power plants in a staged process over the coming years. Now that Scott Bader has successfully developed a new zero styrene gelcoat that also meets all quality criteria for our wind turbine blades, we are a big step closer to achieving this sustainability goal in all our FRP production facilities, and have market leading HSE performance wherever we operate in the world.”
Back in 2012, Scott Bader's then-new 'ultra-low styrene' content gelcoat Crystic Ecogel S1PA was used by LM Wind Power in all its manufacturing facilities, reducing shop floor styrene emissions by more than 50%. LM Wind Power was the first blade producer in the industry to use the new tech.
In future, LM Wind Power plans to switch all gelcoated blade parts moulded around the world to the new zero styrene gelcoat in a managed change process with its end customers.