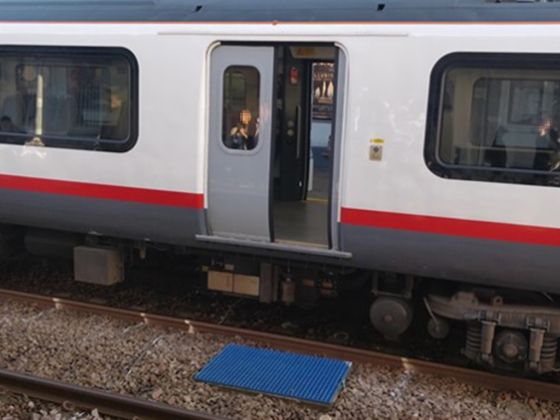
Incorrectly fastened screws resulted in a rush hour train travelling 16 miles while unable to close the doors of a passenger-filled carriage, reaching speeds of up to 80 mph (128 km/h).
The incident led to investigations and the discovery of further loose screws on at least 60 doorways on class 321 carriages in the Greater Anglia fleet.
The incident took place on the 06:35 Greater Anglia Service from London Liverpool Street to Southend Victoria, on 22 August 2019. According to the Rail Accident Investigation Branch (RAIB) report, there was no evidence of abnormal door behaviour before the train stopped at Shenfield station, where the doors in question opened and did not fully close before leaving the station.
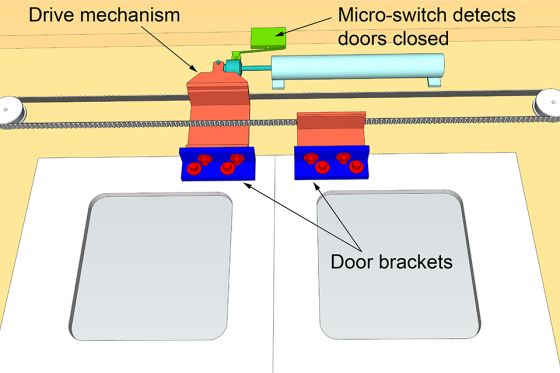
Screws fastening one of the double-leaf doors to the drive belt mechanism that opens and shuts the doors failed - they were found to have worked loose and fallen from the bracket. That left the door free to open and shut according to the motion of the train - including at high speeds.
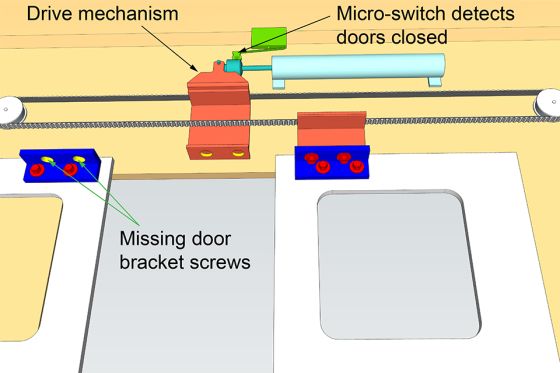
Two loose screws and four wedge lock washers were found by the driver when he opened a panel giving access to door equipment.
Wabtec was named in the report as having refurbished the carriage, including providing new screws for the brackets. A screw torque of 22 Newton metres (Nm) should have been applied, with a second person witnessing the tightening. Yellow marks were supposed to have been applied to the tightened screws, although no such mark was found on the loose screws. The lack of yellow marks was not picked up in subsequent inspections.
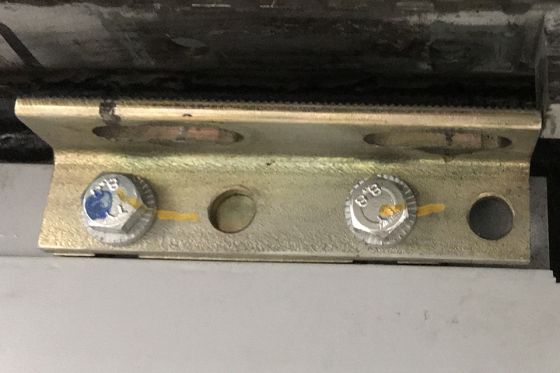
The report also detailed how Greater Anglia maintenance staff used "a plain spanner" to assess screws were still adequately tightened (no torque was specified), relying on "a subjective judgement by staff".
Inconsistencies were also found on the Eversholt-specified torque value of 22 Nm and the 29 Nm recommended by wedge lock washer manufacturer. Those Eversholt recommendations are now being reviewed.
The report details: "Refurbishment by Wabtec included providing new screws for the brackets connecting the door to the drive belt. The fastening arrangement was specified by Eversholt document (EV/VI 3216 Task OR3512) as two screws on each bracket flange with a pair of wedge lock washers fitted beneath each screw head, the aim being to avoid the screw working loose. A screw torque of 22 Newton metres (Nm) was given in an associated Eversholt technical procedure. The specification was dated February 2012 and replaced an earlier version which required a different method designed to prevent loosening of the screws at this location.
"Wabtec required its staff to paint a yellow mark across the screw head, washer and bracket when they had tightened each screw to the specified torque. This assists maintenance staff to identify any subsequent loosening of the screw, as rotation results in misalignment of the marks.
"Wabtec also required that a second person should witness the tightening, check 50% of the screws by applying 80% of the specified torque and then applying a blue dot to the screws which they had checked.
"There were no yellow marks on the two screws which fell from the connection between the bracket and the drive belt, and no yellow mark adjacent to the corresponding holes in the bracket. Both these screws carried a blue verification dot. Yellow marks were present on the screws which secured the bracket to the door and one of these also carried a blue dot."
There's plenty more detail in the RAIB report.
Fastener failures are a relatively common reason for safety recalls (like for Ford USA's recent recall). The issue, particularly related to the automotive market, has led some providers to offer recall-related insurance policies.
Hat-tip BBC.