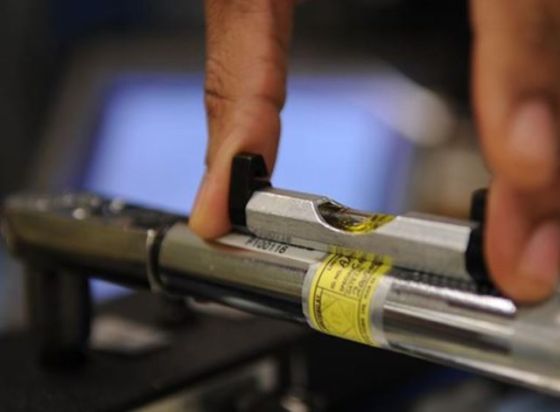
Typically used to torque wheel lugs when changing tires, a torque wrench should always be in sync if you want it to measure the twist and tension of nuts and bolts accurately. Whether you are a race car driver, engine builder or a garage owner, it is very important to have your torque wrench calibrated periodically by a professional for reliable, safe, and accurate results. Torque wrench calibration goes a long way in ensuring safe functioning even with frequent use. You can take any of the following two approaches for torque wrench calibration:
- Doing It Yourself
- Hiring Calibration Services
The DIY approach helps with checking errors that lie within a reasonable range and ensuring that the equipment is properly calibrated. However if the torque wrench is too off the mark and you don’t know how to calibrate an instrument, you can consider hiring calibration services but make sure that the calibration services are accredited to deliver precise and reliable results.
Torque wrench calibration is a time-consuming process but there are special devices available on the market to make the equipment calibration process quicker and simpler. Periodic torque wrench calibration will not only eliminate errors but also keep the torque wrench working at optimal accuracy for longer.
The Risks of DIY Calibration
The torque wrench is an essential component of any precision work, so if you go with the DIY approach, even a slight deviance will offset the calibration enough to loosen a nut, damage bolts, break a stud, or leave behind a stripped thread. If you are working on a high-risk task that mandates complete precision, inaccurate measurements can prove to be dangerous. In order to understand the right torque wrench calibration approach, it is important to know the math behind it – where torque (T) = force (weight) x distance (T = F x D). There are alternative formulas depending on the object that needs to be calibrated.
Any instrument that is not rightly calibrated can adversely affect every aspect – from productivity to safety to quality of the work done. So if you are doing the torque wrench calibration yourself, make sure you do it right if you want the instrument to perform consistently and accurately within the permissible limits. The safest and the easiest way to eliminate errors and ensure complete torque wrench calibration accuracy, is to go with a professional calibration laboratory.
Factors Influencing Torque Wrench Calibration
No matter how careful and meticulous you have been with torque wrench calibration, it is bound to lose precision over a period of time. This is why you must be consistent with equipment calibration to make sure it works accurately and provides reliable results round the year. In order to make the equipment calibration last longer, it is important to understand the following 3 factors that impact calibration:
- Temperature
The average temperature at which the torque wrench is being used will determine the accuracy of the calibration process. Irrespective of whether you work in a hot and humid climate or in cold weather conditions, the measurements must be set to a conductive setting, according to the climatic condition in which it is being used. The right temperature settings play a vital role in reducing errors and ensuring accurate results.
- Values
Torque wrench calibration instructions need to be followed very carefully. Disregarding the manual and deviating from the right values will change the way the instrument behaves which can produce major errors within certain components or even disrupt the entire operating range.
- Tolerance
The quality of calibrator that you are using can impact the end results so it is important to use calibrators that manufactured by reputed and trusted manufacturers or labs. Accredited calibration services employ calibrators that are built to accurate specifications and tolerances to deliver dependable results with repeatable performance.
Inaccuracies and discrepancies in quality control processes can also result due to faulty design and control formulation. This would then result in additional errors that can impact the entire range on which the calibration is performed. Over time, the quality of measurements will deteriorate, thereby lowering the quality of the product. So when you are designing a routine for torque wrench calibration, consider all the regulations that govern your field of operations and check the requirements of the compliance organizations. Check and compare all the standard operating procedures of regulatory authorities and labs and re-calibrate whenever needed. Accredited calibration services that are fully equipped with all the tools, techniques, and technicians to provide equipment calibration services can assure you of reliable results.
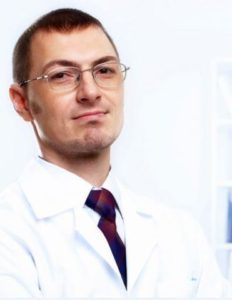
Author Bio: Edward Simpson is a seasoned Calibration and Technical Engineer working for RS Calibration Inc. Edward has a knack for finding faults in machines and does not rest until they are rectified to perfection. He lives in Pleasanton, CA and can be contacted anytime for matters related to machines. He also invites people to visit his company www.rscal.com to learn more about the type of calibration work he does.
There's more on torque tools, including insight into the latest ISO requirements, in Torque's September 2017 Magazine.