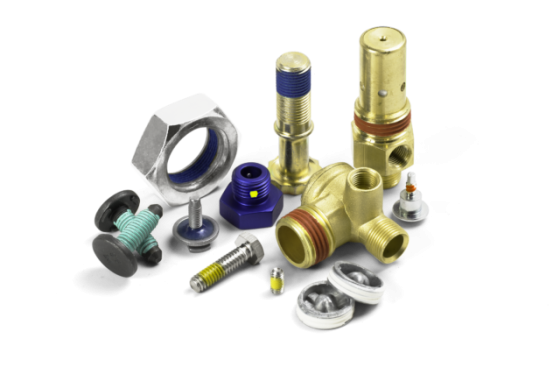
We bring together fastener performance-boosting coating, sealing and plating options available to the market, plus expert comment on the sector.
ND Industries
ND Industries is a manufacturer of solutions for fastener locking, bonding, sealing, masking, lubricating and assembling. ND pre-applies a wide selection of custom manufactured materials onto fasteners, creating point-of-assembly readiness. This results in reduced labour costs, time savings, and quality assurance for our customers. ND Industries has processing centres and licensees strategically located throughout the world. To view the line of available applications, go to www.ndindustries.com
Reinhardt
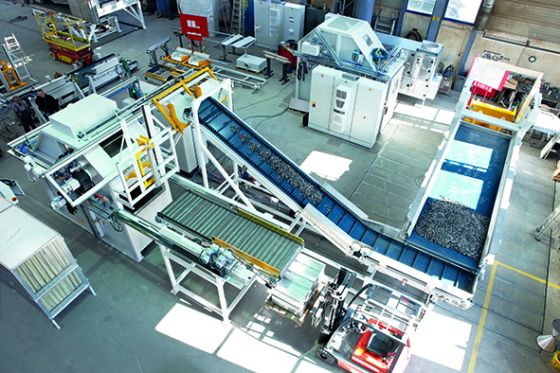
Based in Villingen, Germany, Reinhardt is a global market leader for dip spin coating equipment and reportedly the only supplier to offer two different dip spin technologies for bulk materials complete, for nearly all applications. Complete means Reinhardt is the only manufacturer building its own heat treatment and tempering ovens, backed with 75 years’ experience.
For more than 30 years, Reinhardt has successfully produced industrial coating devices for dip materials, offering machines with capacities up to 6t/h. Big or small charge sizes can be handled and coated efficiently thanks to Reinhardt offering appropriate machine designs. Handling multiple automatic processes consecutively, they are gentle on the materials, with optimal batch separation and low dropping heights.
The patented “Reinhardt barrel” lines boast soft material handling, small paint reservoirs, best coating results with paint scooping parts like Allen head, smallest footprint/throughput ratio, cleaning cycles for barrels up to eight weeks.
Reinhardt dip spin equipment stands for excellent coating results, compact design, fast cycle times, high output and lowest operational cost. The Reinhardt Ovens are said to deliver perfect temperature uniformity, performance and long lifetimes. Website
MacDermid on the optimal torque-tension relationship for fasteners
All fasteners have a designed maximum proof load, which is the largest amount of tensile stress that a component can withstand before it begins to display permanent deformation. Creating the correct torque-tension relationship helps manufacturers to achieve maximum joint security without exceeding the proof load of the fastener, which is particularly crucial in the automated assembly of precision-fastening products. Over the past few years, the requirements for such components have continued to grow, with high demand from industries such as automotive and aerospace.
Zinc and zinc alloys have a relatively high and variable coefficient of friction. This can adversely affect the torque-tension properties of fasteners. Additionally, passivates, which are used to protect the zinc coating from premature white corrosion, also offer different levels of coefficient of friction. For example, those containing hexavalent chromium have an average coefficient of friction of 0.4, whereas those based on trivalent chromium can be as high as 0.5.
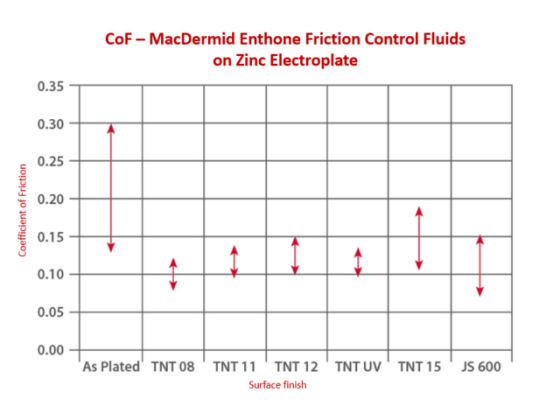
If fasteners are used without a friction control fluid, friction can increase, leading to lower bolt tension in a torque. As a result, the joint weakens, causing poor clamping, insecure joints and possibly premature bolt fatigue failure. Conversely, too much torque can lead to bolt fracture and thread stripping. This factor becomes even more crucial in safety critical applications, such as wheels, seat belts, steering and the suspension component system. Therefore, dry film lubricants are usually applied to zinc and passivated coatings to provide both lower friction and to also make the association more predictable.
MacDermid Enthone Industrial Solution’s ZinKlad® quality assurance program ensures that consistent quality, high-performance coatings are specified by approved applicators across the world. In addition to exceeding the corrosion resistance of hexavalent chromate systems, ZinKlad presents the opportunity for manufacturers to achieve unrivalled consistency and predictable torque and tension characteristics. Website
This article originally appearing in Torque's Digital Magazine for March 2018, which you can flick through online now.