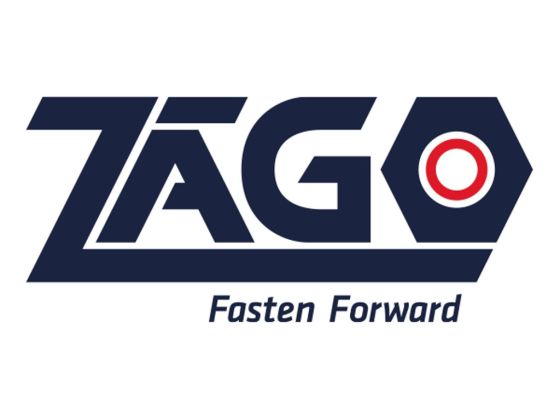
Torque Magazine speaks with Gail Friedberg Rottenstrich, CEO and Co‐Founder of Newark, NJ‐based ZAGO Manufacturing Co., about how ZAGO is meeting increasing demand for its high‐tech sustainable sealing fasteners.
What began as a specialty sealing solution for the military and defense is now critical in myriad industries, including robotics and drones, electric vehicles, manufacturing, LiDAR and others. ZAGO seal screws, seal nuts, seal bolts and seal washers differ from standard fasteners. They are engineered with a custom groove under the head of the screw (face of the nut/washer) that when combined with a rubber O‐ring and tightened, squeezes outwardly to form an impenetrable, 360‐degree seal. This leak‐proof seal prevents contaminants (i.e., oil, water, gas, chemicals, air, moisture, dust) from entering and damaging high‐asset equipment or leaking out into the environment.
With the onset of Industry 4.0, coupled with the coronavirus pandemic, the demand for ZAGO high‐tech sealing fasteners (Made in the U.S.A / Buy American Act compliant) has accelerated. These sealing fasteners protect sensors, electronic components and the data stored on them from contaminants.
“Business this year has been extremely robust continuing a growth trend that has been on an uninterrupted trajectory for the last five years,” says Friedberg. The group has been planning for this rise in production capacity through a combination of automation, robotics, and upskilling talent.
Regarding rises in raw material pricing, Friedberg reports that ZAGO is less impacted by these costs as sourcing has always been an area of strength. “ZAGO is never reliant on only one or two vendors for raw material, but rather can draw from a wide range of vendors, enabling us to negotiate the best possible pricing for ZAGO and our customers,” says Friedberg.
Another area where ZAGO sealing fasteners are in demand is alternative energy and recovery. In addition to sealing out contaminants, corrosion and pressure‐resistant sealing fasteners protect and optimize the performance of offshore wind turbines, solar panels, and fixtures, especially those operating in harsh environments and extreme temperatures.
When it comes to planning the next 12 months, according to Friedberg, ZAGO will continue to increase its production capacity to meet increased customer demand. “ZAGO is both driving and meeting the demand for more resilient, automated equipment to meet current and future challenges,” notes Friedberg.
This article was first published in Torque Magazine. Don’t get the mag? You can apply for a free subscription online today. Or take a look at back issues in the Torque Magazine archive.