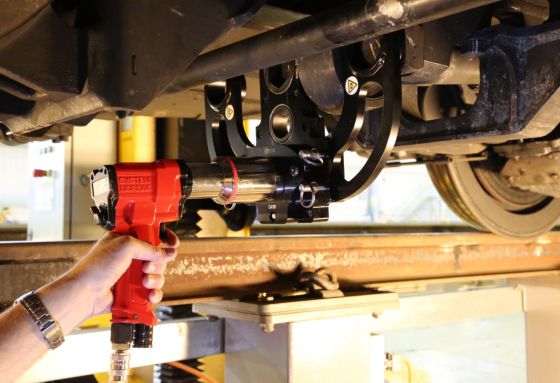
Foreign objects on the track damaged the underside of one of Hitachi Rail’s newly commissioned Class 800 trains, proving a significant maintenance headache for the company. Luckily, help was at hand from Norbar Torque Tools, which produced a bespoke torque solution to solve Hitachi’s problems…
Established in Japan in 1910, Hitachi first came to the UK in 1999 and since then, its innovations have been implemented throughout Britain’s railways. As part of this, it recently replaced a number of aging Class 43 trains with new Class 800 trains for Great Western Railway.
However, when the bogie on one of the trains was damaged by debris ricocheting and rebounding between the track and the under carriage (caused by the vacuum created under high speed trains when traveling at speed), Hitachi Rail faced a potentially lengthy and costly repair process.
A bogie is a safety critical sub-assembly and each carriage has a pair, with one at each end. The bogie is the assembly to which the two axles and four wheels are attached and on a Class 800 train these should be replaced every one million miles or three years. However due to the damage sustained it was imperative that the bogie was replaced immediately.
This was proving no small task. Changing a bogie calls for a bogie drop whereby either the train remains static and the bogie is lowered beneath the train, or, the train is raised and the bogie remains stationary on the rails. It can then be wheeled away and a new one can be fixed in place.
However, another hurdle that maintenance engineers were facing is that the damaged bogie was secured by four traction link fixings, which were bolted and tightened to 970 N.m. Access to these bolts was significantly hampered by the anti-roll bar (ARB) that runs across the width of the train and was located 50mm in front of the bogie’s fixings. This meant that in order to replace the bogie, the ARB needed removing.
This was not only proving time consuming, but also costly as Hitachi Rail’s policy dictates that any fixings removed on a safety critical component, such as the nuts and bolts holding the ARB in position, would also need to be replaced with new ones.

Hitachi Rail therefore needed to find a tool that would enable access to the bogie’s traction link fixings while clearing the ARB and eliminating the need to dismantle it. This is where Norbar’s expertise and a bespoke torque solution kept Hitachi Rail on track.
THE SOLUTION
Norbar was able to take its PTS pneumatic torque tool and create a rapid prototype solution, adding a special offset drive used in conjunction with a FRLUnit. The PTS is part of Norbar’s PneuTorque pneumatic torque tools range and is designed with accuracy and reliability in mind. For this particular job, a purpose designed double ended reaction plate was added, which provided access to the traction link fixings whilst clearing the ARB. This product combination facilitated a straightforward single operation removal and re-assembly of the fixings.
Graham Hudson, Technical Support Engineer at Norbar comments: “Thanks to our in-house ‘engineer to order’ capabilities and rapid prototype solutions, we were able to design and manufacture a specialist solution specific to this application and its requirements. The end result for maintenance engineers is a procedure that is not only safer, but also more time and cost effective.”
Norbar specialises in the manufacture and worldwide distribution of torque tools, for torque tightening, measurement and calibration. Headquartered and produced in Banbury in the UK, there are also Norbar sales, service and calibration facilities in Australia, USA, Singapore, China and India. Other countries are served through a network of distributors.
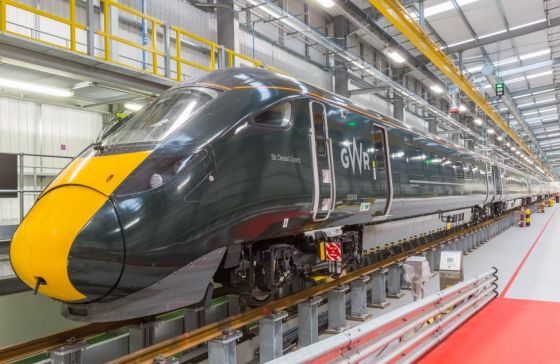