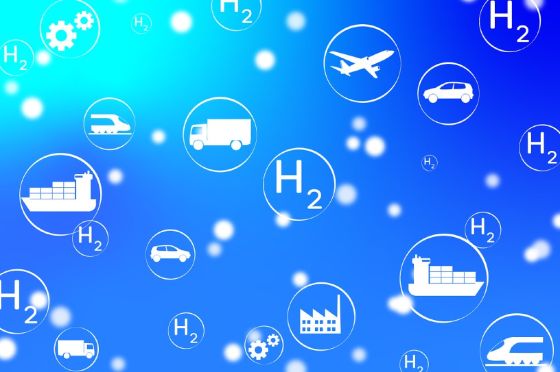
The multinational engineering consultancy, inspection and certification company, RINA, has announced the commencement of the six-year Hydra project to build a 100% hydrogen-fuelled pilot plant. This ambitious open research project will provide ground-breaking near-zero carbon technology and capabilities to the international steel industry.
Funded by the European Commission’s NextGenerationEU plan, the €88M R&D Hydra project is part of the IPCEI (Important Projects of Common European Interest). The hydrogen-fuelled pilot plant will comprise a 30m high direct iron ore reduction (DRI) tower, an electric arc furnace EAF and a reheating furnace that will all operate with near zero emissions for the production of all types of ‘green steel’.
Each tonne of steel manufactured using a blast furnace produces up to two tonnes of CO2. Although the use of an electric arc furnace (EAF) reduces this to 0.68 tonnes, the average for total global steel production currently sits at 1.63 tonnes of CO2 per tonne of steel. The open research Hydra project aims to reduce emissions to mere kilograms of CO2 per tonne of steel and will make this technology available to the industry on the way to net zero.
Ugo Salerno, Chairman and CEO of RINA, says, “The new plant will make the entire steel production process cleaner. It will further provide a fully open testing facility available to steelmakers worldwide to meet the decarbonisation challenge and prove the quality of steel produced using hydrogen instead of carbon-based energy sources.”
The DRI tower, which reduces iron ore (oxide) into metallic iron, will initially run on natural gas. The project team will then assess production using a gas mixture with increasing levels of hydrogen and, ultimately, 100% hydrogen.
The construction of the plant is scheduled for completion by 2025. When fully operational, it will produce up to seven tonnes of steel per hour for research.
“The truly unique nature of this project is its position as an open research facility. It is not intended or designed to provide a commercial advantage to any one steel producer but rather move the industry and the world forward in the use of 100% hydrogen production with near zero emissions. This is why the Hydra project has been supported since its inception by leading European steel producers, plant suppliers, utilities, and major stakeholders in the sector. There are many infrastructure and industry projects underway for the use of hydrogen, and it is hoped this project will also help move these forward by establishing a clear supply chain need within the steel industry.” concludes Mr Salerno.
Ultimately, the technology will rely on the availability of hydrogen to power the steelmaking processes. As part of Hydra, RINA, thanks to extensive experience in hydrogen-based decarbonisation technologies, among which the world’s first test of a 30% gas-hydrogen blend in steel forging, will include a testing and qualification hub of materials and components for H2 transportation and storage and launch an international centre of excellence for the dissemination of hydrogen know-how, fostering collaboration and research among stakeholders in the steel and energy sectors.