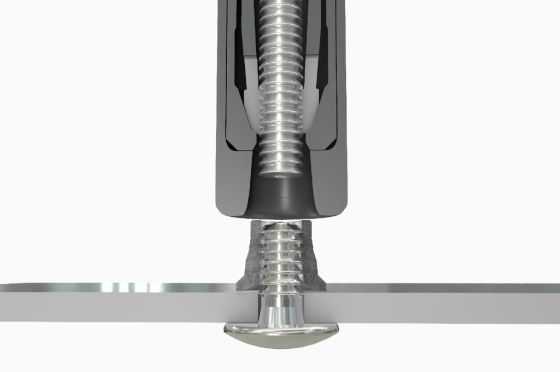
G-Grip is a clever new T304 stainless steel lockbolt system that promises to save on costs
and on time, while also reducing the inventory needed of standard parts. Goebel explains the
benefits of the G-Grip system...
In applications where an extensive grip range is needed and a consistent flush pin break to the collar is favourable, Goebel has devised the G-Grip, pitched as a new and improved standard in the market.
Crucially, the G-Grip can replace up to 14 sizes of the classic 6-groove locking fastener systems, in steel, stainless steel or aluminium.
As with all Goebel engineered fasteners, the G-grip is highly resistant to corrosion and vibration. It features a flush breaking pin, a multi-grip design, an efficient installation process and it reduces the inventory needed of standard parts.
This exciting new development can replace ordinary bolts and nuts with all the accompanying advantages of time and cost savings.
IN STOCK
G-Grip is a patented product, so Goebel Group has full IP rights on this innovation. The ISO 9001:2015 accredited company has a production capacity of nine million pins and nine million collars per month.
What’s more, DIBt and ETA approval will be available soon on the G-Grip, Goebel tells Torque Magazine.
The G-Grip is already proving popular with Goebel customers across a number of sectors, including the truck & trailer industry, agriculture industry, food industry, military industry and automotive industry, among others.
EFFICIENCY, STRUCTURAL INTEGRITY & CONSISTENT CLAMPING FORCES
One of the key advantages of a multi-grip part is improved efficiency in terms of costs, inventory and job site performance through simplified installation. The G-Grip’s extensive grip range and various sizes can replace up to 14 sizes of the classic 6-groove locking fastener system.
G-Grip collar parts and pin are manufactured with polished T304 stainless steel material and on request the pin can be coated with chrome or nickel plating. These newly developed parts therefore offer a high corrosion resistant solution. Stainless steel is famed for its industrial application, particularly in harsh environments, so there are lower maintenance costs and increased structural integrity.
How does the G-Grip offer vibration resistance? During the installation process the collar is swagged onto the pin and locks in place via the grooves. The locking feature guarantees consistent clamping forces, shearing and tensile strength once installed, says Goebel, adding that once the parts are installed, you can be sure the application is secure.
Easy installation with the right tools
As stainless steel is ductile, Goebel was faced with a significant challenge to ensure consistent flush breaking every time. The firm overcame the issue with a patented design which always breaks flush for smooth, safe and simple installation every time.
Goebel offers a comprehensive range of installation tools, ranging from hand tools to cordless battery tools and pneumatic air tools. The best tool for the job for the application depends on frequency of use, explains Goebel. G-Grip lockbolts are installed within seconds (see below) and depending on the
tool used can be set up to 1,200 pieces per hour. It’s easy for the operator to identify a solid flush installation and continue working efficiently, adds the firm.
Installation is easier too, thanks to the reduced inventory required. As the G-Grip extensive grip range and various sizes can replace up to 14 sizes of the classic 6-groove locking fastener system, there’s less need to stock multiple parts for various sizes. At a time when cost efficient inventory systems are vital, G-Grips can save time, space and money through inventory simplification.
G-Grips are available from stock from Goebel, and PPAP Level 3 documentation can be agreed/provided if required.
The firm is currently seeking more authorised distributors to enlarge its worldwide network for the G-Grips. Training is offered (in-house or online) along with support and sales materials, displays, catalogues, samples and full support.
Please contact Thomas.Liebhaber@goebel-group.com to find out more about becoming an authorised distributor.
This article originally appeared in the November-December 2021 issue of Torque Magazine. Read the magazine in its entirety online or subscribe today.

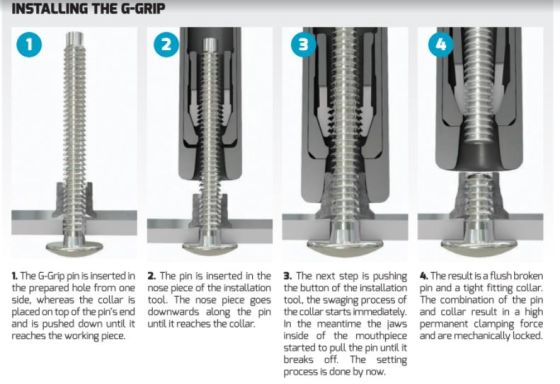