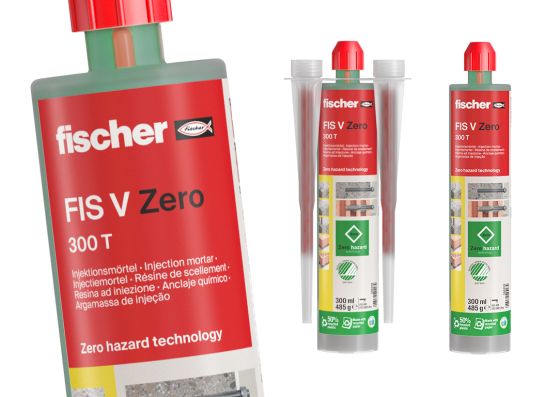
fixing expert fischer now uses more than 50% post-consumer recycled plastic (PCR) to make the cartridges of its FIS V Zero injection mortar. This process has further optimised the packaging of the universal mortar, which is also setting standards in protecting the environment and occupational safety thanks to its non-hazardous formula.
fischer said that more recycled materials are being used in Germany, with the latest survey by Germany’s Federal Environment Agency on ‘plastic recycling in Germany 2021’ using data from the Conversio Market & Strategy consultancy firm. According to the survey, the waste management sector recycled almost all of the 5.7 million tonnes of plastic waste collected in 2021, of which 99.4% were recycled for material or energy purposes. In addition to this, over 0.6 million tonnes of production and processing byproducts were fed directly back into the manufacturing process.
The fixing specialist said it recognised its responsibility for people and the environment along the entire value chain. The company now uses more than 50% recycled
The material used to produce the cartridges of FIS V Zero injection mortar is made of post-consumer recycled plastic (PCR), sourced from a recyclables processor in the form of specified and assessed plastic granulate. In doing so, fischer is complying with the Circular Economy Act of Germany’s BMUV (Federal Ministry for the Environment, Nature Conservation, Nuclear Safety and Consumer Protection), revised in 2020, which aims to establish and expand waste collection and waste management systems and is also supported by the German Chemical Industry (VCI).
fischer is converting all of the available 360 ml and 300 ml FIS V Zero product variants to the new packaging materials. A new 150 ml version is being launched with cartridges made of recycled materials. This new 150 ml version is designed for home users who often only have a few fastening points and won’t be left with unnecessary mortar residue thanks to the smaller container sizes. By optimising its product, the company said it is mastering multiple challenges, as the cartridges for chemical fixing solutions are highly complex technical components of an overall packaging system consisting of up to six parts.
With cartridges made of over 50% post-consumer recycled plastic (PCR), the FIS V Zero injection mortar is reportedly the world’s first non-hazardous injection mortar, according to the EU’s CLP chemical regulation. The product thereby protects the environment as well as the health of those using the product and the buildings it is used in. With its versatile range of potential applications, the FIS V Zero offers the same performance characteristics as other universal mortars. fischer used a new curing system with the FIS V Zero innovation in order to achieve this. No peroxides are used during this process, meaning there is no need for any hazard labels. Combined with the use of non-hazardous raw materials, this mechanism ensures that the FIS V Zero does not require hazard labels even under the strict stipulations of the EU’s current CLP chemical regulation.
The Eurofins Indoor Air Comfort Gold certificate confirms that the injection mortar fulfils the highest requirements to maintain clean indoor air quality with VOC content and VOC emissions ((Volatile Organic Compounds). The product is certified in accordance with the Nordic Swan Ecolabel, the official ecolabel of the Nordic countries, which identifies products that are particularly environmentally friendly. fischer also received the Federal State of Baden-Württemberg’s Environmental Technology Award in first place in the Emission Reduction, Treatment and Separation category for its FIS V Zero injection mortar in 2021, confirming the fixing solution’s high degree of innovation in protecting the environment and people using the product. The environmental impact of the FIS V Zero injection mortar is described in its Environmental Product Declaration (EPD)(EPD-FIW-20230531-CBA1-DE). The injection mortar’s EPD assessment is based on life cycle assessment data verified by independent organisations and takes the product’s entire life cycle into account.
A long journey from idea to implementation
fischer’s R&D team has been looking into sustainable cartridges for a long time. “While developing our cartridges made of recycled material, we overcame many challenges in the development department of our Denzlingen site and explored various options,” said Amir Assadi, Developer in the fischer Chemical Business Unit. “We were assessing the use of wood-plastic composites (WPC) as early on as 2013. As a result, we examined the market acceptance of post-industrial recycled (PIR) and mass balance plastics made from alternative raw materials. We even considered mechanically processing empty injection mortar cartridges.”
A feasibility study carried out by fischer on recycling empty containers showed that recovering and reprocessing fischer’s own empty cartridges from large-scale construction sites opened up new opportunities for conserving more resources and additional recycling. One of the disadvantages, however, is the need for additional transportation. In its pilot project, the fixing expert collected used cartridges from construction sites in an elaborate process before processing them together with a service provider, during which labels were removed and the cartridges were crushed to flakes before being washed and melted down into new plastic granules. Advantages of a centralised system include fewer transport routes and the ability to process larger volumes of recycled materials with scalable labour and energy consumption. fischer therefore considers it to be more sustainable and cost-effective to join the existing circular economy.
By considering sustainability in addition to the safety of the environment and product, the company will continue to optimise its products throughout the value chain.