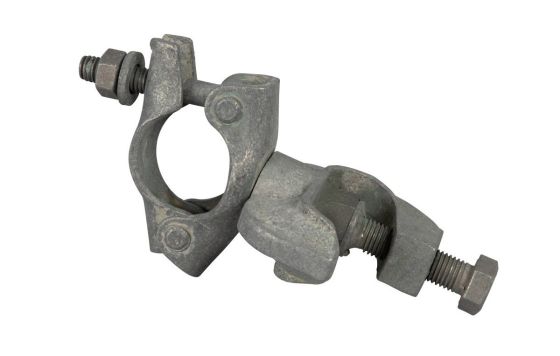
Sustainability has been causing some business challenges of late, not least as the industry grapples with current and sometimes shifting CBAM legislation, but the need for sustainable product is growing demand for high performance coatings as firm's look to boost their eco-credentials. That's according to Anochrome Group, which notes renewed interest in advanced coating techniques - particularly thermal diffusion coating.
Steve Norman, Group UK Divisional Director at Anochrome Group, sad that trend has been seen connected to industries including oil and gas, wind energy and defence.
Thermal diffusion is an advanced solution that offers superior protection, extending the lifespan of metal parts and enhancing performance, said the firm.
The process diffuses zinc into steel at elevated temperatures, forming a robust anti-corrosive alloy layer on the metal's surface. This method, also known as thermal diffusion galvanizing, utilises a zinc alloy powder to create a protective coating for ferrous-based parts.
The result is a hard, non-magnetic coating that provides exceptional resistance to corrosion, oxidation and abrasion, outperforming traditional protection methods.
Steve Norman said: “In industries where metal components face harsh environments, safeguarding against corrosion and wear is paramount.
“If parts last longer, that ultimately leads to a more sustainable product – and that is a core consideration for decision makers across most sectors. It also, of course, reduces maintenance costs and helps to ensure optimum performance.
“We have definitely seen a noticeable uptick in thermal diffusion enquiries from right across Europe. This specialised coating is extremely difficult to come by, so we would expect demand to continue to increase.”
Anochrome Technologies can offer thermal diffusion coating with a range of PFAS free zinc flake topcoats that enhance the application and lifecycle performance, while ensuring compliance with evolving sustainability regulations, and evolving coating standards such as ISO 12944.
Thermal diffusion coatings have demonstrated over 1,000 hours of salt spray protection, significantly outperforming traditional hot-dip galvanizing, Anochrome said. This can be significantly increased by a topcoat application of zinc flake technology. The coating also provides excellent abrasion resistance and prevents seizing, even on stainless steel components. Thermal diffusion coating is free from heavy metals and complies with REACH regulations, making it safer for both users and the environment, it added
Steve added: “Thermal diffusion can be used in C5 environments with very high corrosivity, which are typically industrial areas with high humidity and aggressive atmospheres, as well as coastal regions with high salinity.
“It can also be an option in CX environments with extreme corrosive environments, particularly offshore areas and with structures exposed to extreme humidity, aggressive atmospheres and tropical conditions.”
Thermal diffusion can be used to enhance fasteners, couplings, bolts, components and critical hardware across the rail, wind energy, solar, aerospace, marine, construction and energy sectors.
There's more information via sales@anotec.co.uk