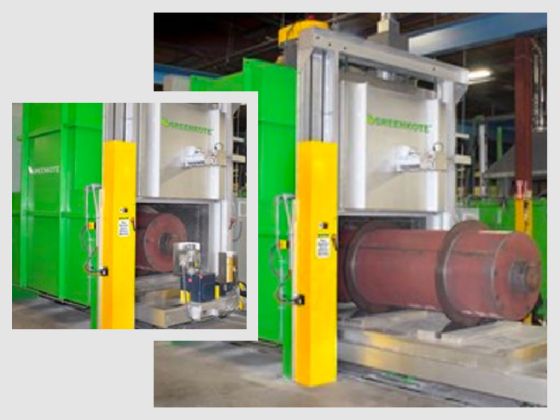
Greenkote, global provider of advanced anticorrosion metal coatings, has announced a major expansion of production capacity at its headquarters facility in Brook Park, Ohio.
The expansion comes in response to an upsurge in demand for corrosion protection on environmentally exposed metal fasteners and hardware in a number of different industries.
Mark Gore, CEO, said: "I don't know if climate change may be a part of it, but we're seeing notable increases in anticorrosion coating orders for all kinds of different metal parts that are exposed to the elements."
"The orders are coming from a range of sectors, including automotive, rail, electric power distribution, wind power generation, and others. These are all applications that have fasteners, fixtures and other metal hardware exposed to long-term outdoor atmospheric corrosion."
“It's also possible that we're getting more than our share of this business because of a couple other factors," added Gore. "Number one: Greenkote coatings are actually diffused into the metal surface, making them damage resistant, longer-lasting and better-performing than older treatments such as galvanizing and paints. Another factor is eco-friendliness. Many other coating processes involve acids and other polluting chemicals, so their use is increasingly restricted by environmental regulation. But, as the name implies, Greenkote is uniquely benign to the environment."
Gore stated that installation of the additional coating equipment in Brook Park has been completed and the facility is now fully operational with significantly expanded capacity.
Greenkote provides anticorrosion coating services for construction, automotive, rail, utilities and many other industries in which parts are exposed to weather or harsh and corrosive environments. Greenkote can be applied to a broad range of metal parts, from threaded fasteners to stamped and cast pieces, in sizes from 0.2 to 78 inches.
Proprietary Greenkote coatings have been replacing several older anticorrosion processes such as galvanizing, hot-dip, sherardizing and metal flake. In addition to increased corrosion protection, Greenkote technology provides superior adhesion, longer wear, and more conformal coverage, which allows its use on complex geometries such as small threaded parts. Greenkote also eliminates metal failures caused by hydrogen embrittlement, an intrinsic problem with many traditional coatings.
Greenkote is applied by a patented zinc-based dry thermal diffusion process that requires no hazardous chemicals and produces no toxic byproducts. Consequently, it is uniquely friendly to humans and to the environment.
Are you in the fastener, tool, fixing or related industries? You can subscribe to Torque Magazine or sign up to our weekly newsletter.