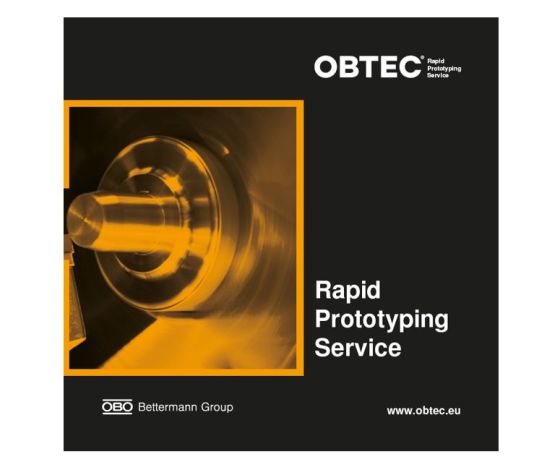
OBTEC’s new prototyping service launched at the end of 2018 but has already seen projects go into production in the automotive sector, with interest afoot in the construction and electrical sectors too. Head of Sales Stephan Wennrich takes Torque through the service…
Last year, Menden-based OBTEC launched a new service to get custom product into the hands of its customers faster than ever.
The Rapid Prototyping Service combines speed with economically efficient product development, specifically of fastening elements in small quantities.
Based on customer specs, OBTEC makes prototypes – which are partly machine cut – and checks them in terms of their practicality, suitability for series production and their profitability. Thanks to the skills and knowledge of the OBTEC team, both speed and the standards have been fast and at the highest quality.
Customers using the Rapid Prototyping Service receive a feasibility check for large-scale production as a cold-formed part and proposal drawings for an economically viable cold- formed part. Short-notice, partly machine cut prototypes can be made as a functional model, close to series standard and available materials include steel, stainless steel, aluminium or brass – in lengths of up to 100 mm virtually anything is possible.
The offering has already gone down well since OBTEC launched it in the autumn of 2018, explains Stephan Wennrich, Head of Sales: “The service has been very well received by our customers since the beginning of the year. In fact, we’ve also seen the first customers commission smaller series of turned parts.
“We are able to produce prototypes from one piece. The service usually makes sense to maximum of 5,000 pieces. As a rule, we can deliver prototypes within a maximum of two weeks. It can take up to 16 weeks for the parts to later become cold-formed parts.”
[gallery ids="12886,12887,12888"]
What kind of products is OBTEC offering the prototype service with? “Almost all products are possible, which we will later deliver in series,” Wennrich says. “There will also be a small series of turned parts.”
Drawing on the experience of the team to optimise prototypes is core, he adds: “That's our declared goal. We want to support our customers directly in the development phase.”
So far the service has been used largely in the automotive sector, where several prototypes have gone into production. Customers from the construction industry and the electrical
industry have also taken early advantage of the service.
The new Rapid Prototyping Service has got underway during a positive trading performance for OBTEC, adds Wennrich: “Our total turnover after closing of the first quarter of 2019 is almost 13% above the previous year. Currently, we expect to maintain this level until the end of the year.”
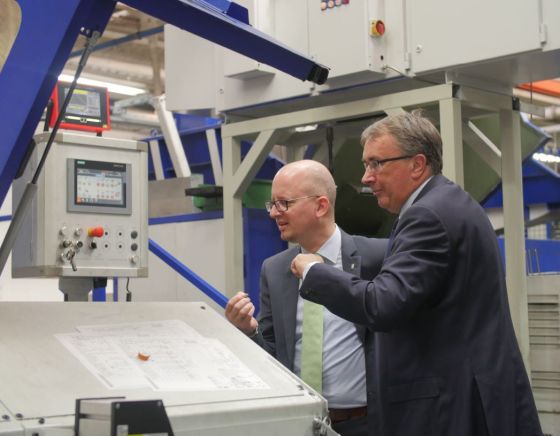
Wennrich also lifted the lid on some intriguing future developments from the firm: “We are currently working hard to establish our welding studs and special screws on the Russian market. For this purpose, we have set up our own sales department in Lipetsk since May 2019, which will be focusing on the acquisition of new customers in the second half of the year.”
OBTEC's range of services now includes injection elements for plastics.
There's more on OBTEC's history here.