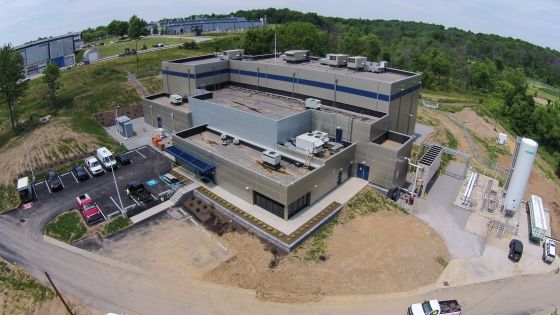
Lightweight metals player Alcoa has opened a state-of-the-art, 3D printing metal powder production facility near Pittsburgh, Pennsylvania.
Alcoa will produce proprietary titanium, nickel and aluminum powders optimised for 3D printed aerospace parts at the facility, which is located at the Alcoa Technology Center, reportedly the world’s largest light metals research centre.
Metal powders used for 3D printing durable, high-quality aerospace parts are only available in limited quantities so this expansion is intended to remedy this with Alcoa developing materials with the specific properties needed for 3D print high-performance components. The firm has also invested in a range of technologies to further develop additive processes, product design and qualification.
“Alcoa is forging a leadership path in additive manufacturing with a sharp focus on the critical input material—metal powders,” said Alcoa Chairman and CEO Klaus Kleinfeld. “We are combining our expertise in metallurgy, manufacturing, design and product qualification to push beyond the possibilities of today’s 3D printing technologies for aerospace and other growth markets.”
The facility will form part of Arconic following the recent separation of the company.
Alcoa has been in the 3D printed product business for 20 years. The plant is part of a $60 million investment in 3D printing, building on the Company’s 3D printing capabilities in California, Georgia, Michigan, Pennsylvania and Texas. Thanks to its acquisition of RTI, it now has printing capabilities in titanium and other speciality metals for aerospace and other growth markets. Airbus recently selected Alcoa to supply 3D printed titanium fuselage and engine pylon parts for commercial aircraft, with the first additive manufactured parts to be delivered later this year.